Not much to say, but a lot to look at!
Scheme designed by Plane Schemer
Paint by Evoke Aviation
Photos by Jonathan McCormick
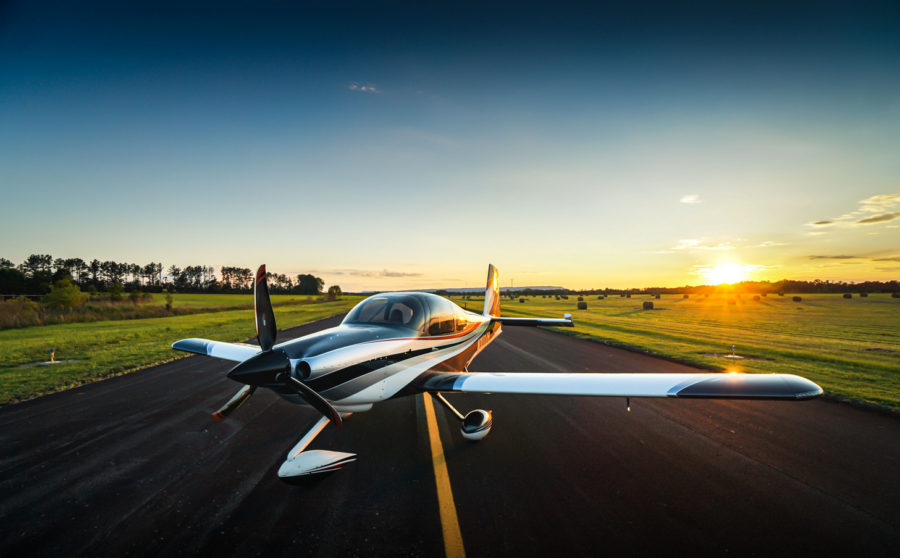














Not much to say, but a lot to look at!
Scheme designed by Plane Schemer
Paint by Evoke Aviation
Photos by Jonathan McCormick
Several (four-five?) years before first flight, I met this little guy named Jonathan McCormick who has a scheme design and paint business in Alabama. Plane Schemer and Evoke Aviation are his life’s work and they are simply put amazing. Here’s a brief story of how we got Tess all dolled up.
I met Jonathan at Sun N Fun in 2015 and got to work with him on designing a scheme. I was early in the build but wanted to have some motivation and vision on what we were putting together in the garage. He was great to work with for a reasonable fee and didn’t stop until I gave the final approval on every little detail. We started with some inspiration photos that I sent him and some descriptions of each aspect that I like and wanted to incorporate. He then took this and put his artistic skills to work creating a truely unique and exiting paint scheme.
We wanted something no one else had and something different than a typical cheat line or a few swooshes. My main inspiration came from another RV, this one having 8 wheels and two slide outs used on the road. He really nailed the design with the tail and the whole scheme grew from that feature. Laura loves orange, and it’s high on my list of favorites, so we decided that would be the splash of color in the scheme. We went back and forth with a few things, lines here, swooshes there, wheel pants reversed, etc. When it was all said and done, we had a one of a kind paint scheme that was going to be a head turner. I also had motivation to stop cruising the internet for plane pictures and finish building.
But wait, there’s more! Sam, Jonathan’s girlfriend and business partner, has a side business creating custom artwork. Laura and I wanted a little logo we could use for the plane, shirts, cups, seats (didn’t get to put it on the seats), pillows, basically anything that can be embroidered! She and I worked together to create a custom logo for the plane and I couldn’t be happier with the result. We will incorporate that into the paint as well as all kinds of fun stuff. I do politely ask that our logo not be copied, as Sam earned a commission on this artwork and Laura and I would like to keep this unique to our plane.
Fast forward a few years and airshows later with a random meeting in Raleigh NC on the ramp, I reached out to Jonathan about getting a slot for painting the plane. He and I agreed it’s best to paint after flight tests, as stuff comes on and off a lot plus a few adjustments can be made without messing up the paint. In March of 2020, I flew Tess down to Gadsden, AL (KGAD) airport to drop her off for paint. Jonathan and I spent the morning doing a tour of his two facilities, checking out other projects, and poking our heads into warbird jet projects on the field. He also finalized the actual colors in his office and did just a few tweaks on the scheme after having a few years and hundreds of other designs now under his belt.
I left knowing it’d be a few months before it’s all finished up and let him and his team go to work. This website doesn’t have room to describe all the work they did! It does have room to say how good the work was! Wow, they dove in deep and with a vengeance for perfection. All of my stupid little new builder mess ups were corrected, they smoothed and perfected the fit of the wingtips which needed a lot of work, and they did an amazing job prepping each and every surface for a perfect paint job. The amount of filling and sanding was mind blowing to me even after I thought I had done a decent job of prepping. With the amount of colors and layout of the scheme, it was also a ton of work to get the color on the airplane. I still can’t figure out which order they put the colors on but the results were mind blowing. With the status pictures coming in with all the color on, I thought we were close to the finish line, but that’s where even more work comes in. They wet sanded the entire airplane, knocking each line down between colors and eliminating all waves, orange peel, and imperfections. Then, they cleared the entire plane. One smooth consistent surface makes a massive difference on the quality and longevity of the paint job. Buffing and touch-ups were next and then I got to come down and help put it back together. We finished the windows with sealant filling the troughs in around the edges and a protective bead on the bottom of the windshield. The guys were great hosts, taught me a few things, gave me a lot of help, and lots of new shiny stainless steel hardware!
Even our tug got a cool paint job from a new painter learning his skills. Honestly, the tug gets more comments than the plan does at home!
After several agonizing months without a plane, we rolled Tess out into the evening sun for a photo shoot on the taxi way. I was drooling the entire time! To say I’m happy is a massive understatement and the feedback from others is the same. Even after a year of flying and a few scratches, sorry Jonathan, I still get people coming up to it everywhere I go commenting on the paint.
So, the nitty gritty of it all. It was expensive. Really expensive. It took a long time. A lot longer than I was told originally and was expecting. It is better than I could have ever imagined. It is worth twice what we paid for it. I’m realizing that even more with fellow builders struggling with paint quality issues. I have and will continue to recommend Evoke and the team of professionals to everyone because they doe the job right the first time.
Jonathan, you took our baby girl and made her beautiful. Thank you!
I will document the biggest and most annoying things wrong with the airplane during the test flight here but do not plan on blogging about every repair or modification to the airplane. Mainly because I’d have to become a full time writer.
The flight tests went fairly smoothly and I finished the 40 hour phase 1 in under a month. Most of my issues were builder caused, I must admit. Either a rework or bad soldering, decision making or lack thereof, and a few “that’s good enoughs” that came back to haunt me were to blame.
I tracked these by creating a list in my phone/iPad that I could check off as I corrected the issues. The list kept growing for some time before it started getting checked off. It’s worked really well for me and actually motivates me to complete all the repairs or adjustments to get the check boxes checked. I can also make group entries into the logbook to keep track of the work.
I found that I had a lot of electrical gremlins throughout the first bit of flying. Solder sleeves are amazing little buggers that are notoriously difficult to use correctly. I used sparingly while building, but they still bit me a few times. The problem is you think the solder ring has melted completely but it hasn’t. The connection will be good until it’s subject to some vibration and then all kinds of weird things happen. My oil pressure spiked to 200 PSI, multiple random annunciations based on my discrete inputs, and a few others due to the solder sleeves. And I only have about 10 in the whole plane! I will use them now if I have good access to the connection, but if not, I’ve found using Dsub pins and heat shrink as more reliable.
I had to reposition my EGT probes, as I realized they blocked 5 out of 6 spark plugs. I had a master cylinder bolt leaking just a bit. Lots more clamps and zip ties were installed, mostly firewall forward, to avoid chafing after a few oil changes and seeing where things moved a bit too much. I had to replace the autopilot pitch servo due to a service bulletin, roll servo due to slipage, and had to reinforce the rudder trim tab mount to get it to work effectively. I chose to rewire a few engine switches and add a engine master switch, which I should have done in the first place. That all neccessitated under the panel work, a new switch panel overlay and backlight sheet. The oxygen system leaked above 1200 psi (loose connection), and a few adjustments to the door light switches have been made.
The biggest squawk is a leaking fuel tank. I am getting ahead of myself on the blog, but this was discovered post paint unfortunately. Turns out a little weeping rivet that I discovered prior to paint and thought I had fixed with the Loctite trick wasn’t fixed. In fact, it wasn’t a weeping rivet, but a pinhole in the sealant on the rear baffle. Fortunately, I spent an entire day and was able to use my borescope to provide a view and a coat hanger/tube of pro seal to apply sealant and fix the leak without taking the tank off. Not a fun job.
The engine ECU tweaks were pretty easy, although I’ve gone through four O2 sensors (leaded fuel doesn’t make them last long). I removed the air filters and just installed a mesh screen over the intakes. Speaking of intakes, one was too close to the exhaust header and a hole burned through it so that required a bit of glass work along with better heat insulation and a bit more clearance.
Lots of other tweaks and adjustments were made and most of these delayed discrepancies were taken care of during the first condition inspection performed in November last year. I do have a few more items to check off the list including new door hing covers, some finish rework on the interior windshield pillars, an intake plenum on the air conditioning condensor (more on that later), and adding a second tunnel access plate are all on the list for 2021.
Bottom line, you’re not done building when you’re done building. Flying brings on new stuff that you can’t forecast on the ground so it’s a continuous process to keep it in tip top shape. I also put some of this stuff off, as I wanted to get it flying so its been a challenge to get caught up after flying so much. I am now at a point where the regular maintenance time is decreasing vs the flight time increasing. The check boxes are all most all filled in!
Since I now have an airplane, the next logical step is to fly it right? Kick the tires and light the fires! Dad, Laura, and I celebrated the certificate with a nice dinner full of phone calls and texts from friends, family, and well wishers. This community is simply amazing. So many people congratulating us on our accomplishment like we are old friends. Some we haven’t even met in person!
Mark Ciaglia and Charlie Derk have especially been motivators to me. Mainly, I want to build a better plane than both of those losers and no doubt I have. We have a group text running back years at this point full of questions, this is what I did, that’s stupid I’d never do it that way, and remind me never to fly in (fill in the blank)’s plane. Seriously though, these guys have been such a rock to lean on for advice, ideas, encouragement, and comradery. They both have amazing RV-10s in the works and no doubt will be amazing accomplishments. Anyway, not to get too sappy, we received an awesome gift in the mail that required a signature with a note that only Mark and Charlie could come up with. Thanks guys, I hate you too.
Dad and I put everything back together on the plane the next day with gloomy skies preventing the temptation of first flight. We spent some time going over the plane again just to quadruple check everything. I also gave dad his first ride in the plane when I towed it down to the compass rose to calibrate the ADAHRS and magnetometer. He did great and didn’t even get sick. Something tells me the 20-something-thousand hours as a pilot contributed to his courage and brake-riding expertise! When we ran out of things to check, we called it a day and put her to bed one last time before she flies.
Friday, November 15th dawned with partly cloudy skies and light winds with a small chance for isolated showers. The weather was good, the plane was ready, and I was out of excuses. So my ground crew consisting of Dad, Laura, and Parish all headed towards the hangar ready to fly. Laura set up the camera as Dad and Parish established comms with a handheld radio and took up station next to the runway. I did another pre-flight inspection and had some solo time with the plane before strapping in.
Using the EAA test flight cards, the first flight is all about ensuring the plane flies well and beginning to break in the engine. Keep the power above 80%, keep the temps as low as possible, and stay within gliding distance until confident there’s no big issues. Dad and I worked out a plan for me to take off and orbit the pattern at 3000′ while shaking down the plane and engine. If any issues popped up, I’d land. If I felt good, I’d head towards KEHO then to KHKY and return back to KIPJ after an hour and a half. This provided good access to landing spots and kept me away from trouble like towers and mountains. Vic assigned a 100 NM radius test area so I had plenty of room. Coming back home, I’d do a practice approach at 2000′ testing flaps then land on the second approach.
So, I strapped into Tess, patted her on the glare shield and cranked her up. A long taxi to the south end of the field and a salute from Dad helped me get all the nerves out before doing my runup and entering the runway. Check out the videos for takeoff and landing below and excuse the childlike squeals and giggles (and language) from the pilot.
Needless to say I had the RV grin! Overall the flight went well. The plane handled beautifully and I felt that the flight was conducted in a safe manner. It was not squawk free, however! Fellow builders will understand that the excitement of success is quickly overwhelmed by the anxiety to fix issues. So here are my big take aways from the first flight:
Highlighting the important things, the engine ran smoothly and man was it powerful! The temps all stayed below 400* which means that my hard work on baffles and plenum is paying dividends. It was fast! Much faster than I was expecting! Almost everything worked, or at least worked well enough!
The smoke was a huge Oh Shit moment for about a second or two but quickly mitigated itself. I’m sure others would disagree, but I decided to continue the flight because I was confident in what was causing it. When we purged the preservative oil out of the engine, I had not hooked up the scat tubing to the heat boxes or muffs. I had tried to soak up some oil from the heat muff but it’s hard to get a rag down in there. When I smelled the odor and noticed it didn’t continue, I put even more focus on the engine gauges and felt safe to keep flying.
The configuration issues will be sorted in time, although they are annoying, I’m not too worried about them. My biggest embarrasment was the audio panel and radio communication. With all of the playing and testing of things, I had it in my head that the AFS radio (integrated with the EFIS) was Comm 1 and the Avidyne GPS/VHF was Comm 2. Quite the opposite. Not being comfortable with button pushes and menus quite yet meant that I constantly transmitted on the wrong radio. CTAF was on Comm 1 and Dad was on Comm 2.
A huge thank you goes to every single person who has lent a hand, gave advise, answered a question, banged a rivet, help lifted something, and gotten dirty to enable me to achieve this dream. My biggest supporter, my wife, Laura, has been by me every day of this and I truly could not do it without her. I’m so glad my Dad could come up and be a part of this day, as it’s one of my proudest and to be able to share it with him, where my aviation passion stemmed from was icing on the cake.
Just to prove the landing was awesome, my Bianca Bro, Todd Kincer, caught the evidence from the ground. I’ll never make a better landing in the plane and that’s okay!
After a several day weather delay, Vic arrived on a clear sunny morning, November 13 2019, in his RV-10. Vic had given me some homework to accomplish before he arrived and I had all of it plus extra paperwork all prepared in the hangar. I used the EAA kit to register the aircraft and was thankful for the guidance with the paperwork, as it doesn’t always make perfect sense. He also requested certain panels removed and let me know what could stay assembled pending anything noticed during the inspection.
First, we sat down and did the paperwork. There’s quite a bit but he’s got a great program and process to accomplish it all in an orderly fashion. Everything was in order and I had my first logbook entry for him to review. I also had my build log website ready for him to look at, but learned he had been following along already (even though it wasn’t updated completely).
After the paperwork was done, we started a thorough walk through of the plane. He certain has his hot spots to look for and went straight to them. I think since he was able to follow along with my build and see my progress, it helped speed up the inspection. My work looked really nice to him as we went through the wings and even got a compliment on my riveting! While he does a great inspection, he also relies on the builder to do fundamental testing. We didn’t do a control surface check with the digital level nor an engine start which I thought would be required, but he did check it all over with a fine toothed comb.
My proudest moment was when he told my dad later in the morning that “No kidding, it is the cleanest install that I have ever seen.” Now, I’m sure he tells all the builders that, just like the doctors tell dads that their kid is the best! But I still appreciated such a flattering comment from the King Vic!
Of course, he can’t sign off everything without finding a few things! I had some wires still needing a few more zip ties just to prevent chafing. He also suggested a few tips for the rudder trim which I’ll upgrade in the future. The biggest issue was my data plate. I had heard horror stories of failing the inspection only because the builder’s name was incorrect. I made sure to follow the directions to a tee in the EAA guide. Unfortunately, I took for granted that Last Name (comma) First Name equals First Name Last Name. On the forms, it tells you to put Huneycutt, Tim S. So that’s what I did thinking they know Tim is my first name. On my data plate, it said Tim S Huneycutt. Wrong. Registration says Huneycutt, Tim S so that’s what the data plate has to say.
Fortunately, Vic saved the day after he ruined it (kidding, Vic) by whipping out a blank data plate and letting me hand engrave it with the correct verbiage. I immediately ordered a new one with professional engraving that I’ll put on after paint.
So yeah, time for the obligatory handshake photo! I pulled Tess out of the hangar and put her nose to nose with a veteran RV-10 for a photo opp. Squinting into the sun, Vic handed over my airworthiness certificate and our 6 year long build project just became a real airplane!
I decided to ask Vic Syracuse to do my inspection, as he is renowned for his RV-10 knowledge and experience not only by building several of them as well as maintaining them with his business, but also by inspecting hundreds previously as a DAR. This inspection is performed on behalf of the FAA and results in an airworthiness certificate allowing first and subsequent flights. Basically, it’s the final exam of the building process. One that you should study hard to be ready.
One of the ways I’ve been studying is getting other people to look and help lately. Dan Olson who flies a Glassair and is an A&P has been a huge help in hanging the engine, brake bleeding, and final support before inspection. I’ve also had countless others stop by poke their heads in and ask questions which helps me look at things with fresh perspective. I also decided to host a little gathering of my EAA chapter one evening for a show and tell as well as find something wrong!
We had a great turn out and lots of discussion about the plane and other projects. A handful of little things were discovered, but it turned mostly into a social event, which is half of the fun! Pizza filled everyone up and the night was over after a lot of enjoyment and good conversation.
My dad came up from Florida for a few days to help with final prep and to be my ground crew during first flight. While his intentions were always good, Dad loved smacking his head into the horizontal stabilizer. Three times. Once was so hard I swear he dented the damn thing. In the end, Tess scored three times and dad zero. He was banished to the corner of the hangar with a bloody forehead and a headache. I still love ya Pop. We tested out the back seats just for the fun of it.
The last task was to rivet my data plate on and apply the registration. It’s almost an airplane!
Okay, so if you really pay attention, the pictures and story isn’t exactly in chronological order. So sue me.
The airworthiness inspection is rapidly approaching and it’s crunch time now. This post is about as fast and deep as all the stuff I had to do.
The awesome guys on based helped me bend my control sticks to provide plenty of clearance to the instrument panel. I still hit the flap switch in the full nose down, right roll position, but if I ever have to use that stick input, I have way more concerns about dying.
I never installed the tips on the stabilizers, so I wiped the decade old dust off of those and riveted them on then laid up some glass to enclose them. Some tweaking with the heat gun was enough to get them adequate clearance and I’ll let Jonathan do the rest of beautifying them during paint.
I crawled in the tail cone. Again. After I said, “Oh, I’m done back there, I won’t need to get back there.” Hell, at this point I can’t even remember why I had to go back there. I’ll flash forward and tell you that still wasn’t the last time. Either way, here’s how I feel about doing that little shit job.
The rest of the interior went in and lights hooked up. These side panels are pretty tricky to slide in without destroying the paint. I’m happy with how they turned out. The stainless screws also look really nice.
I pulled the plane out for a good GPS and comm check. I’ll have another post about the details, but while everything worked, I have some serious interference with the ZipTip lights and my radios. For now, though, no night flying means I’m safe and legal to fly.
The back seats and carpet are all in now. I had to put a lot of velcro down but man, this Aerosport stuff is amazing. The seats are comfortable, the carpet looks great, and I’m really excited about taking folks flying in this plane!
My cover from Bruce’s came in and is freaking sweet. Fits very nicely, has orange, and the tail number embroidered on it makes it so no one can steal it and use it on their plane without me chasing them down.
I put the cowling on for a final fit check and hooked up the new AeroTherm engine heater. I’ve used these on the Diamond we fly and really like it. I didn’t like the idea of cylinder heaters and want to keep the engine heated during the winter to avoid cold starts. I know this isn’t as portable, but I’m happy with it thus far. I did have to get a very thick extension cord so it would keep tripping its internal breaker with my crappy 15 amp service in the hangar.
Finally, I weighed the fat little piggy with all of the pants and random stuff not yet on for good in their approximate place. Folks, with full interior, oxygen, air conditioning, three screens up front, and all the extras my credit rating could buy, I’m pretty happy with her girlish figure. This let me sit down and compute weight and CG figures as well. Everything turned out nicely with an empty CG of 106.4 inches.
Ahhh, the day is upon us, my dear friends. First engine start! Builders dream of this moment then quickly wake up in a panic sweat from the nightmares of “oh shit, what did I forget” or “how can I instantly destroy my $XX,000 engine before it even flies?”. Needless to say, I was nervously excited.
The afternoon started off with removing the lower plugs and purging the cylinders of the remaining preservative oil. Most had drained out but I was really surprised at how much was still in there. By spinning the engine/prop with the starter and no spark plugs (top coil disconnected as well), it purges the cylinders as well as creates oil pressure in the engine for first start.
It took five or six cycles lasting around 5-10 seconds each to finally build oil pressure. I suspect it might have been less had something not been awry, but I’ll get to that in a moment. Either way, I left a nice stain of oil splattering on the ramp and celebrated when we saw a positive number on the oil pressure gauge.
By the time we reinstalled the plugs, put the EGT probes back in place (yep, I drilled them where they block the plugs which will have to get corrected eventually), and did yet another final check of the engine, it was dark and cold. I pulled the plane out and Laura pointed the car headlights while Dan and Todd observed from either side. I won’t spoil the ending, so click play below and enjoy the show!
She’s alive!!!! Bam, pow, fireworks, roars to life! Ah, the sound of a new born baby gurgling and screaming, not sure if that’s normal or the onset of disaster. It’s normal, folks. But not everything was perfect. The common practice of hand tightening an oil filter on a car or anything else for that matter does not apply to aviation. The filter wasn’t torqued and I had a pretty good stream of oil escaping, possibly affecting us getting the initial pressure indication as well. We pushed her back into the hangar and got to work cleaning up.
The second start was better. While it didn’t sound perfect, the engine started and ran well. Dan had helped me set up the timing light so we could set the magnet position on the flywheel with the SDS ECUs. This step is no longer required by SDS but I feel that getting it custom set with your exact setup will result in a better tuned engine, especially when running LOP and advanced ignition. We set the position pretty easily and it already sounded better. I also remembered to turn the alternator on after a few minutes which really helped charge the battery!
The SDS system does not use a mixture lever thus you have to shut the engine off in a different manner. Ross suggested simply turning off the electric fuel pump which would kill the engine (no mechanical pump). The first time I did this, the engine continued to run for a good 30 seconds. I’m still not sure why, but subsequent runs and testing results in a timely shut down just as pulling the mixture lever would do. By the end of the third idle run, we were all freezing, tired, and ready to call it a night. The engine is alive, healthy, and leak free!
First engine start is very close now with only a few punch list items left to complete. The biggest and most important item is bleeding the brakes. Other builders seem to have mixed results with this process, some knock it out in 10 minutes and others just drag their feet while landing having completely given up on ever having effective braking abilities thanks to the ridiculousness of the task. It appeared as if I was going to join the latter group.
Kitplanes had a great article about bleeding from the calipers up. This makes sense as it forces all of the air out of the system as the fluid enters. One caveat for my system, however, are the Beringer master cylinders which prefer to be horizontal while bleeding to ensure the air actually escapes. That meant diving head first into the foot wells and disconnecting them from the rudder pedals. I had forgotten how many little washers and spacers were used in their assembly. Ugh.
Amazon Aircraft Supply Co, Inc, LLC, R with a little circle around it, delivered a brake bleeding tank that many people recommended vs. the small hand pump bottle that doesn’t quite deliver enough pressure to complete the job. I ran down to another popular aviation hardware distribution company, Lowes, and picked up some clear tubing and a few fittings and valves. The idea is to view the fluid, bubble free, entering the caliper and then exit into the brake reservoir on the firewall. The valve allows you to control the flow of brake fluid while tightening the bleeder screw in the caliper. Pretty easy to set up and I’d highly recommend it.
I also got a fitting to screw into the brake reservoir that accepted more of the clear tubing. When bleeding, you want to see the air come out of the reservoir followed by bubble free fluid. Once you see that, the system is bled and should have good pressure. Of course, it wasn’t that easy to get what you see below.
The right side of the system bled easily and took almost two and a half minutes. This led to a sense of cockiness and confidence that only I can exhibit while moving to the next and saying wow, this is going great! The left side brought me back to the humble earth by making a fool out of me. No matter what, we could not get the left side bled. Fluid would go in to a point but never show evidence of reaching the reservior. Likewise, we could not get adequate pressure using the master cylinder nor see any difference in the level of fluid in the reservoir. The master cylinders would also not force fluid out of the caliper as they should either. Something was wrong.
My buddy Dan, who was helping and hated the process as much as I started to, suggested breaking the seal on fittings moving up the line to see where the suspected blockage is. Fortunately, we were lucky and found it at the fitting on the bottom of the fuselage near the gear leg. Fluid moved easily up to that point but would go no further. So I disconnected the line from the tunnel to that fitting and took a closer look.
It seems that while building I neglected to cover those fittings and a little bastard insect built a fine home in that line. After taking my air hose with 100 psi set on the regulator to the hose, I wound up with this mess finally popping out of the brake line.
Well, that would explain why fluid would not move one way or another. After reassembling the line, it took almost two and a half minutes to bleed the left brake. This after about two hours of screwing around with it and a LOT of cussing. I also managed to piss of my hangar neighbor by telling him this wasn’t a good time for someone to come in and check out the project. Sorry dude, hope you get over me asking you for a rain check. Either way, air was replaced with fluid, the pedals were put back together with much grunting and back pain, and I could finally put the brakes on this build.
There is a lot of little projects yet to be completed on the firewall forward section, so I set about tackling them. First off was safety wiring the prop bolts. I thought torquing them were hard. Well safety wiring them is even worse. Because of the limited space, you actually have to loosen them a bit, thread the wire through the hole, then re-torque them. Ugh. Anyway, it’s not pretty but it’s done. I’m convinced this flange design negates the need to safety wire since they’d all have to unscrew in perfect unison for the damn thing to fall off anyway.
Here is a picture of the custom wrenches I had made up using Joe Key’s templates.
Since I was at the front end, I went ahead and finished up the spinner installation. The back plate takes some time to bolt on as well with 1300 bolts used to hold it to the prop hub. The spinner has three plates behind the blades to fill the gaps and it took a bit of dry fitting to figure out where each one goes. WW had labeled them by number and I was wrongly lining them up with blade numbers not just the reference number on the spinner and back plate. The front of the prop hub fits into a bulkhead in the spinner and it took a few iterations of Teflon tape and sanding to get a nice snug fit with no wobble of the spinner.
The air filters were the last step for the intakes and I had been waiting on a different filter with a tilted base, allowing clearance of the tube to the filter assembly itself. This was required because of the blister I had to glass in for the air conditioning compressor. Fortunately a 10* tilt made just enough clearance and it all fit together nicely. I oiled the filters and got them put on for good or at least until the first annual.
The right intake tube is close to the exhaust, so I used some heat shielding that has an adhesive back to protect the tube. I went back and covered this with 3M foil tape and then applied RTV around the edges to secure it. I’ll monitor this during ground runs to ensure enough protection from the exhaust header.
Since I had RTV all over me anyway, I took the opportunity to finish seal up a few spots around the engine and firewall. I have spent a TON of time trying to find any little spot air could leak out of the baffles that it shouldn’t be leaking. Since the hangar is dark with the lights off, I again used a flashlight on top of the engine to highlight any little spots. It worked great and I’m hoping it pays off with adequate cooling once flying. It’s impossible to be super clean and fancy with this stuff, but I kept most of the mess on me instead of on the engine.
So many of my electrical connections are oddly shaped so getting a boot to fit hasn’t been easy or even possible. I used a 3M product to paint electrical tape onto the hot studs just to keep a surprise shock chance low. Not quite as good as boots, but better than nothing.
Lots of zipties up front still being added as I just see spots here or there that could use some extra security. I may add wire wrap that is rated for high heat to clean it up, but not sure if I care or want to spend the time on that quite yet.
Multi-tasking is key at this point so I setup the vacuum pump on the aircon system while RTV was setting up. All of the lines and connections are secured so I could finally vacuum the system to perform a leak test and evacuate moisture from the system. The ports are just behind the baggage bulkhead and pretty easy to get to. I set up the pump and let it run for about an hour and a half to get moisture out then closed the pump off and let the gauges sit all night long. The next day I returned to see a perfect vacuum still holding, so that is a huge win!
The last two projects up front were some additional glass work on the plenum and a ramp for the aircon compressor. The plenum was designed to be sealed to the cowl around the oil dipstick, but I didn’t like the idea of air potentially leaking out of the plenum through the oil door or into the engine area. I cut up a sports drink bottle as a mold and roughed up a little funnel to fit over the dipstick. The dipstick will have some foam tape sealing the bottom of the funnel. It didn’t come out as pretty as I wanted, but it’s functional and I can always clean that up a little down the road.
The air ramp was a little easier than I expected. On the left side intake, the aircon compressor causes the cooling ramp and induction intake to need a cutout and I wanted to create a little blister to help direct all the air possible into the cooling and intake ducts. I shaped a foam block and used packing tape to secure it to the cowl. I used some carbon fiber to lay up a rough fairing then cleaned up the edges after it set up. This is attached via two screws and should provide a nice air flow deflection that is simple to use. I plan to create a final piece of bulb seal to fully seal the cowl to the engine portion helping minimize air pressure loss while providing flexibility for engine movement.